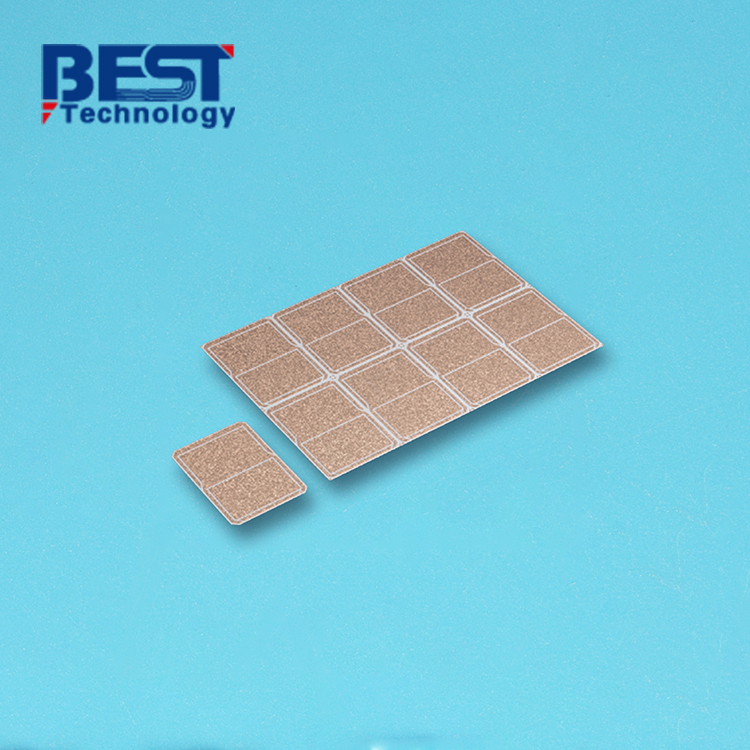
AMB Ceramic PCB Design Fabricaiton For IGBT






|
AMB (Active Metal Braze) Ceramic PCB is by using active solder to achieve the bonding between copper foil and ceramic substrate, through the selection of active solder can reduce the bonding temperature (less than 800°C), and then reduce the internal thermal stress of the ceramic substrate.
1.Material: Al2O3, AIN, Si3N4
2.Function: Ceramic PCB that use AMB technology characteristic as higher thermal conductivity, copper adhesion, lower thermal resistance and higher reliability.
3.Type: Brazing technology.
4.Custom service available.
Background:
Faster Electronics, a renowned company specializing in high-performance IGBT design and manufacturing, faced a challenge when their customer expressed concerns about insufficient thermal dissipation capabilities in their present IGBT chips. This limitation hindered the performance of their motor drivers. In their quest for a solution, they identified the potential of Si3N4 AMB ceramic substrate as a promising base material for their IGBT chips. However, they lacked a reliable supplier capable of manufacturing AMB ceramic components. Consequently, they sought the expertise of an experienced manufacturer to address this issue.
Project Challenges:
Insufficient thermal dissipation: The existing IGBT chips were unable to adequately dissipate heat, negatively impacting motor driver performance.
Lack of a reliable AMB ceramic supplier: Faster Electronics faced the challenge of finding a trustworthy manufacturer capable of producing AMB ceramic substrates to meet their specifications and quality standards.
Solution:
Recognizing the criticality of the challenge, we collaborated closely with Faster Electronics to develop a tailored solution using AMB ceramic circuit boards for their IGBT chips. Our approach encompassed the following steps:
Extensive consultation and evaluation: We thoroughly understood Faster Electronics' requirements and specifications for the AMB ceramic substrate, taking into account their thermal dissipation and reliability needs.
Customized AMB ceramic manufacturing: Leveraging our expertise in ceramic technology, we employed advanced manufacturing techniques to produce AMB ceramic substrates that aligned precisely with Faster Electronics' specifications. The substrates were meticulously designed for optimal thermal dissipation and electrical performance.