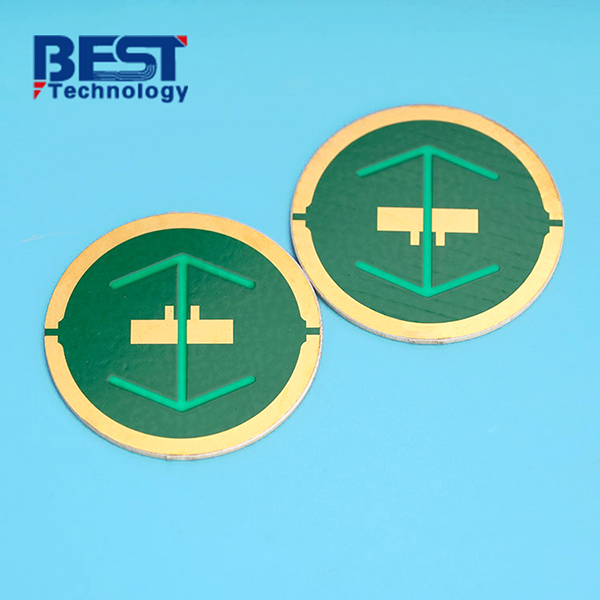
Solar Energy Application Ceramic Substrate Design AlN DPC PCB






Board thickness: 1.0mm+/-0.1mm
Conductor: 105um copper on both sides
Solder mask: Green Glass Glaze
Silkscreen: N/A
Surface finishing: ENIG 3u’’
Application: Solar energy application
Item1 | DPC Capabilities | |||||
---|---|---|---|---|---|---|
Layer Count |
1-2 Layers |
|||||
Max Board Dimension |
120mmx180mm | |||||
Min Board Thickness |
0.15mm |
|||||
Max Board Thickness |
6.0mm |
|||||
Conductor Thickness |
50/50μm |
|||||
Min Line Width/Line Space |
3/3mil (0.075/0.075mm) |
|||||
Substrate Type |
AI2O3, ALN, Si3N4 |
|||||
Substrate Thickness |
0.15-6mm |
|||||
Min Hole Diameter |
100μm |
|||||
Min Hole Spacing |
250μm |
|||||
Min PAD Ring(Single) |
0.125mm |
|||||
PTH Wall Thickness |
8um |
|||||
Min Solder PAD Dia |
0.25mm |
|||||
Min Soldermask Bridge |
Green Oil 130μm; Others 150μm |
|||||
Min BAG PAD Margin |
0.3mm |
|||||
PTH/NPTH Dia Tolerance |
0.05/0.075mm |
|||||
Hole Position Deviation |
50-75μm |
|||||
Outline Tolerance |
Laser: +/-0.13mm |
|||||
Line Width/Spac Tolerance |
±20% |
|||||
Surface Treatment |
OSP/Immersion Gold/Nickel Plated Gold/Immersion Silver/Nickel Plated |
|||||
Thermal Stress |
7.3pmm/k |
Item2 | Attribute | ||
---|---|---|---|
Brand |
CeramTec / GTT / Huaqing / Laird / Maruwa / Rogers / Toshiba |
||
Base Material |
AI2O3 |
||
Base Material Thickness (exclude conductor) |
0.15-6mm |
||
Thermal Conductivity |
24-170W/mk |
||
Soldermask Type |
Aluminum Oxide |
||
Tg Value |
800℃ |
||
Halogen Free |
No |
||
Breakdown Voltage |
15 KV/mm |
||
Dielectric Constant (MHZ) |
9.4 (1MHz); 9.1 (13GHz) |
||
Water Absorption |
≤0.5% |
||
ROHS |
Yes |
||
Flammability |
Grade A |
||
Thermal Conductivity (W/m.K, or W/m.C) |
24-170 W/mk |
||
Dielectric Strength |
>15 KV/mm |
||
Wrap & Twist |
3% |
Prototype(<1m²) | Layers | Normal Service | Expedited Service |
---|---|---|---|
DPC Ceramic PCB |
1 Layer |
DPC: 2 - 3 weeks |
DPC: 1.5 weeks |
2 Layers |
DPC: 2 - 3 weeks |
DPC: 1.5 weeks |
Production | Layers | Normal Service | Expedited service |
---|---|---|---|
DPC Ceramic PCB |
1 Layer |
DPC: 3 - 4 weeks |
DPC: 1.5 - 2 weeks |
2 Layers |
DPC: 3 - 4 weeks |
DPC: 1.5 - 2 weeks |
DPC ceramic PCBs are primarily used in power electronics, where efficient heat dissipation is crucial. They are commonly found in devices such as power modules, power converters, inverters, and high-power LED lighting.
Properties of DPC ceramic PCB
- Good heat dissipation performance, stable working temperature, suitable for all products with good thermal conductivity
- High mechanical strength, good thermal conductivity, excellent insulation
- Good adhesion and corrosion resistance
- Good wear resistance, up to 50,000 times
- High reliability
DPC Ceramic PCB Specification:
Substrate material: |
AlN |
Board thickness: |
1.0mm+/-0.1mm |
Conductor: |
105um copper on both sides |
Solder mask: |
Green Glass Glaze |
Silkscreen: |
N/A |
Surface finishing: |
ENIG 3u’’ |
Application: |
Solar energy application |
Background:
Our customer, SolarEnergia Ltd., is a manufacturer of solar modules for residential and commercial installations. They are committed to delivering high-quality, efficient, and durable solar panels to meet the growing demand for renewable energy solutions. As an industry leader, SolarEnergia continuously explores innovative technologies to enhance the performance and reliability of its solar modules.
Recently, they faced a significant challenge in optimizing the performance and lifespan of their solar modules. Traditional materials used for the circuit boards in solar modules had limitations in terms of heat dissipation, environmental resistance, and dimensional stability. These limitations resulted in reduced energy conversion efficiency and a shorter overall lifespan of the solar modules.
Solution:
When SolarEnergia viewed our website, they reached to us and asked for what they wanted and their challenges and concerns. After analyzing together, we proposed the adoption of DPC ceramic circuit boards in their solar modules. DPC technology offers superior thermal conductivity, excellent environmental resistance, and exceptional dimensional stability. These features make DPC circuit boards an ideal solution for the demanding requirements of solar module manufacturing. We designed and fabricated the ceramic PCB with expedited service, and finally, customer received the boards within 2.5 weeks.
In addition, due to the copper foil covering a large area on the ceramic PCB surface, our operator put the un-vulcanized paper between each board to avoid the boards be oxidized.
Result and Benefits:
SolarEnergia expressed great satisfaction with the implementation of DPC ceramic circuit boards in their solar modules. The improved heat dissipation capabilities of DPC technology resulted in an average energy conversion efficiency increase of 3%, leading to enhanced overall system performance. They said we are the only one ceramic PCB supplier that they want to cooperate again in China.