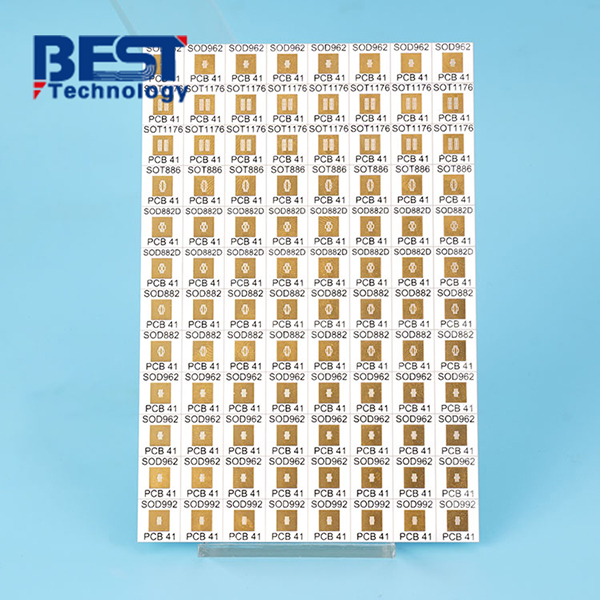
Double-sided Laser Equipment DPC Ceramic Circuit Board






Board thickness: 1.0mm+/-0.1mm
Conductor: 70um copper (top), 35um copper (bot)
Solder mask: N/A
Silkscreen: Black
Surface finishing: ENIG 1u’’
Application: Laser equipment
Item1 | DPC Capabilities | |||||
---|---|---|---|---|---|---|
Layer Count |
1-2 Layers |
|||||
Max Board Dimension |
120mmx180mm | |||||
Min Board Thickness |
0.15mm |
|||||
Max Board Thickness |
6.0mm |
|||||
Conductor Thickness |
50/50μm |
|||||
Min Line Width/Line Space |
3/3mil (0.075/0.075mm) |
|||||
Substrate Type |
AI2O3, ALN, Si3N4 |
|||||
Substrate Thickness |
0.15-6mm |
|||||
Min Hole Diameter |
100μm |
|||||
Min Hole Spacing |
250μm |
|||||
Min PAD Ring(Single) |
0.125mm |
|||||
PTH Wall Thickness |
8um |
|||||
Min Solder PAD Dia |
0.25mm |
|||||
Min Soldermask Bridge |
Green Oil 130μm; Others 150μm |
|||||
Min BAG PAD Margin |
0.3mm |
|||||
PTH/NPTH Dia Tolerance |
0.05/0.075mm |
|||||
Hole Position Deviation |
50-75μm |
|||||
Outline Tolerance |
Laser: +/-0.13mm |
|||||
Line Width/Spac Tolerance |
±20% |
|||||
Surface Treatment |
OSP/Immersion Gold/Nickel Plated Gold/Immersion Silver/Nickel Plated |
|||||
Thermal Stress |
7.3pmm/k |
Item2 | Attribute | ||
---|---|---|---|
Brand |
CeramTec / GTT / Huaqing / Laird / Maruwa / Rogers / Toshiba |
||
Base Material |
AI2O3 |
||
Base Material Thickness (exclude conductor) |
0.15-6mm |
||
Thermal Conductivity |
24-170W/mk |
||
Soldermask Type |
Aluminum Oxide |
||
Tg Value |
800℃ |
||
Halogen Free |
No |
||
Breakdown Voltage |
15 KV/mm |
||
Dielectric Constant (MHZ) |
9.4 (1MHz); 9.1 (13GHz) |
||
Water Absorption |
≤0.5% |
||
ROHS |
Yes |
||
Flammability |
Grade A |
||
Thermal Conductivity (W/m.K, or W/m.C) |
24-170 W/mk |
||
Dielectric Strength |
>15 KV/mm |
||
Wrap & Twist |
3% |
Prototype(<1m²) | Layers | Normal Service | Expedited Service |
---|---|---|---|
DPC Ceramic PCB |
1 Layer |
DPC: 2 - 3 weeks |
DPC: 1.5 weeks |
2 Layers |
DPC: 2 - 3 weeks |
DPC: 1.5 weeks |
Production | Layers | Normal Service | Expedited service |
---|---|---|---|
DPC Ceramic PCB |
1 Layer |
DPC: 3 - 4 weeks |
DPC: 1.5 - 2 weeks |
2 Layers |
DPC: 3 - 4 weeks |
DPC: 1.5 - 2 weeks |
DPC Ceramic PCB is a type of printed circuit board made from ceramic materials with a copper layer directly plated onto the ceramic substrate. Based on the thin film technology, the metallization of the ceramic surface can be achieved by magnetron sputtering, and the thickness of the copper layer is greater than 10um by electroplating.
1. Material: Al2O3, AIN, ZrO2, Si3N4
2. Function: It has a lower coefficient of thermal expansion and higher conductivity, the small size makes it in a very narrow space.
3. Type: Thin film technology.
4. Custom service available.
DPC Ceramic PCB Specification:
Substrate material: |
96% Al2O3 |
Board thickness: |
1.0mm+/-0.1mm |
Conductor: |
70um copper (top), 35um copper (bot) |
Solder mask: |
N/A |
Silkscreen: |
Black |
Surface finishing: |
ENIG 1u’’ |
Application: |
Laser equipment |
Background:
Dallint electronics is a manufacturer of laser devices that used in various industries, including medical, industrial, and research sectors. In laser devices, the performance and efficiency of the circuit boards play a crucial role in ensuring accurate and stable laser output. The customer faced challenges with their existing circuit boards, such as limited thermal dissipation, signal degradation, and inadequate durability, which impacted the overall performance of their laser devices. With a commitment to delivering cutting-edge laser technology, the customer sought a supplier who enables to provide high quality circuit boards that can help to improve the performance and reliability of their laser devices.
Project challenge:
- Customer don’t have a gerber file, and they don’t know what kind of ceramic circuit board is suitable for their project.
Solution:
After constant communicating and analyzing with customers, they decided to implement the proposed solution using DPC ceramic circuit boards in their laser devices. The new design incorporated the advanced features of DPC boards to address the challenges they had been facing.
In their experiment, the DPC ceramic circuit boards were integrated into the laser devices, replacing the previous PCB materials. The enhanced thermal conductivity of DPC boards efficiently dissipated heat generated by the laser components, maintaining stable operating temperatures and preserving laser output accuracy.
Additionally, the improved signal integrity of the DPC ceramic circuit boards minimized signal loss and distortion, ensuring precise laser beam control and reliable performance. The mechanical durability of DPC boards provided resistance to external factors, increasing the overall reliability and longevity of the laser devices.
Result and Benefits:
Our customers are very satisfied with our products and services, and now all the circuit board in their laser equipment were supplied by us.