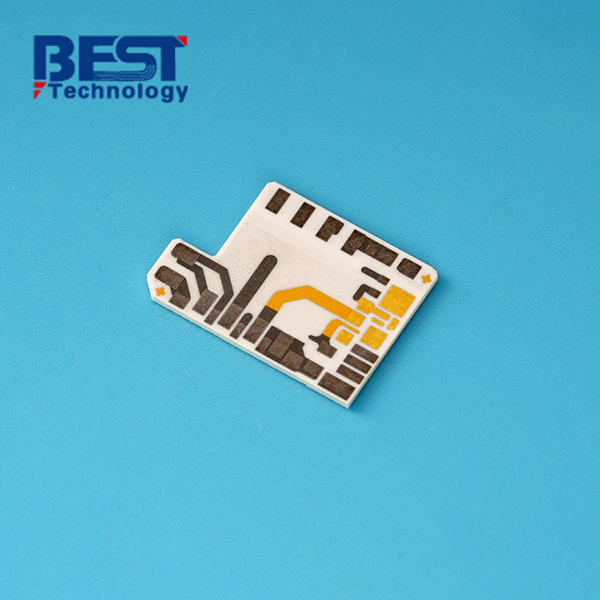
LTCC Ceramic Substrate PCB Design Prototype For Power Amplifier






Board Thickness: 1.0mm
Conductor: 0.1umTiW+3.0um Ni
Solder Mask: N/A
Silkscreen: N/A
Surface Finishing: N/A
Application: Vehicle Electronics
Item1 | LTCC Capabilities | |||||
---|---|---|---|---|---|---|
Layer Count |
4-64 Layers |
|||||
Max Board Dimension |
150mm×150mm |
|||||
Min Board Thickness |
Single layer 0.1mm, total thickness 0.15mm |
|||||
Max Board Thickness |
Single layer 0.25mm, total thickness 6mm |
|||||
Conductor Thickness |
6-12μm (the surface layer can be thickened to 80μm) |
|||||
Min Line Width/Line Space |
150μm (surface layer can be refined to 50μm) |
|||||
Substrate Type |
Al2O3 |
|||||
Substrate Thickness |
0.15-6mm |
|||||
Min Hole Diameter |
100μm |
|||||
Min Hole Spacing |
250μm |
|||||
Min PAD Ring(Single) |
0.125mm |
|||||
PTH Wall Thickness |
N/A |
|||||
Min Solder PAD Dia |
0.1mm |
|||||
Min Soldermask Bridge |
75μm |
|||||
Min BAG PAD Margin |
0.635mm |
|||||
PTH/NPTH Dia Tolerance |
10μm |
|||||
Hole Position Deviation |
30-40μm |
|||||
Outline Tolerance |
Laser cutting: 0.005; Die stamping: 0.005 |
|||||
Line Width/Spac Tolerance |
±20% |
|||||
Surface Treatment |
Immersion Gold/Nickel Palladium Gold (Surface treatment is not recommended) |
|||||
Thermal Stress |
7.3ppm/K |
Item2 | Attribute | ||
---|---|---|---|
Base Material |
DP951,DP9K7, Ferro-A6-M |
||
Base Material Thickness (exclude conductor) |
0.15-6mm |
||
Thermal Conductivity |
17W/mk |
||
Soldermask Type |
Aluminum Oxide |
||
Tg Value |
800℃ |
||
Halogen Free |
No |
||
Breakdown Voltage |
9.4 (1MHz); 9.1 (13GHz) |
||
Dielectric Constant (MHZ) |
≤0.5% |
||
Water Absorption |
0% |
||
ROHS |
Yes |
||
Flammability |
Grade A |
||
Thermal Conductivity (W/m.K, or W/m.C) |
17W/mk |
||
Dielectric Strength |
15KV/mm |
||
Wrap & Twist |
0.003 |
Prototype(<1m²) | Layers | Normal Service | Expedited Service |
---|---|---|---|
LTCC Ceramic PCB |
6 Layers |
6 - 8 weeks |
3 - 4 weeks |
8 Layers |
6 - 8 weeks |
3 - 4 weeks |
|
10 Layers |
6 - 8 weeks |
3 - 4 weeks |
|
>10 Layers |
6 - 8 weeks |
3 - 4 weeks |
Mass Production | Layers | Normal Service | Expedited service |
---|---|---|---|
LTCC Ceramic PCB |
6 Layers |
7 - 9 weeks |
4 - 5 weeks |
8 Layers |
7 - 9 weeks |
4 - 5 weeks |
|
10 Layers |
7 - 9 weeks |
4 - 5 weeks |
|
>10 Layers |
7 - 9 weeks |
5 - 6 weeks |
Why Best Technology?
Best Technology is thrilled to be your trusted business partner. Our primary objective is to be the leading and most professional PCB manufacturer worldwide, specifically catering to prototyping production. With over a decade of experience in the field, we are fully committed to satisfying the diverse needs of our customers across various industries. Our dedication extends to ensuring exceptional quality, timely delivery, cost-effectiveness, and fulfilling any challenging requirements you may have. As one of China's most seasoned ceramic PCB manufacturers and PCB assembly specialists, we take pride in being your ultimate business partner and reliable friend for all your PCB demands. Our goal is to streamline your R&D processes, making them effortless and efficient.
1. Material: Al2O3, AIN, Si3N4
2. Function: LTCC can be embedded with multiple passive devices through multi-layer interconnection, and combined with surface mount technology to achieve active-passive integration, greatly improving the assembly density of the circuit. Meanwhile, the dielectric constant can be controlled by changing the material, which increases the flexibility of circuit design.
3. Type: Co-fired technology.
4. Custom service available.
Background:
TechPower Solutions is a manufacturer of high-power amplifiers used in communication infrastructure. They were facing challenges in achieving efficient thermal management and compact design for their power amplifiers, which were crucial for their market competitiveness. They approached us with the objective of improving the performance and reliability of their power amplifiers. They required a solution that could effectively dissipate heat, reduce signal losses, and enable miniaturization of their amplifier modules.
Solution:
As a leading LTCC ceramic PCB supplier, we provided a comprehensive solution to address TechPower Solutions' challenges. Our team of experts collaborated closely with their engineering team to understand their specific requirements and design custom LTCC ceramic PCBs. Our Professional Approach:
Expertise in LTCC Design: With our extensive experience in LTCC technology, we utilized advanced design techniques to optimize heat dissipation and signal integrity within the power amplifier modules. Our in-depth knowledge of LTCC materials and manufacturing processes allowed us to deliver high-performance solutions.
One-Stop Service: We offered a complete range of services, from initial design and prototyping to volume production and testing. By providing a comprehensive one-stop service, we ensured seamless project execution and minimized lead times for TechPower Solutions.
Customer-Centric Approach: We placed a strong emphasis on understanding TechPower Solutions' needs and exceeding their expectations. Our team actively engaged in continuous communication, providing regular updates and incorporating feedback throughout the project. This customer-centric approach ensured a successful collaboration and a solution that precisely met their requirements.
Result and benefit:
We successfully delivered LTCC ceramic PCB solutions that addressed the thermal management and compact design challenges faced by TechPower Solutions. The collaboration resulted in enhanced performance, improved reliability, and a competitive edge for their power amplifiers in the market.