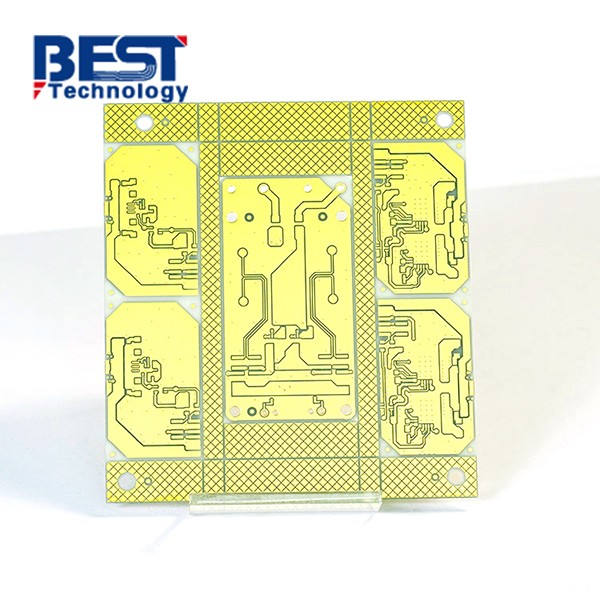
96% Al2O3 DPC Ceramic Substrate PCB Design Production For Sensor






Board thickness: 0.25mm+/-0.1mm
Conductor: 35um copper
Solder mask: N/A
Silkscreen: N/A
Surface finishing: ENEPIG 3u’’
Application: Sensor
Item1 | DPC Capabilities | |||||
---|---|---|---|---|---|---|
Layer Count |
1-2 Layers |
|||||
Max Board Dimension |
120mmx180mm | |||||
Min Board Thickness |
0.15mm |
|||||
Max Board Thickness |
6.0mm |
|||||
Conductor Thickness |
50/50μm |
|||||
Min Line Width/Line Space |
3/3mil (0.075/0.075mm) |
|||||
Substrate Type |
AI2O3, ALN, Si3N4 |
|||||
Substrate Thickness |
0.15-6mm |
|||||
Min Hole Diameter |
100μm |
|||||
Min Hole Spacing |
250μm |
|||||
Min PAD Ring(Single) |
0.125mm |
|||||
PTH Wall Thickness |
8um |
|||||
Min Solder PAD Dia |
0.25mm |
|||||
Min Soldermask Bridge |
Green Oil 130μm; Others 150μm |
|||||
Min BAG PAD Margin |
0.3mm |
|||||
PTH/NPTH Dia Tolerance |
0.05/0.075mm |
|||||
Hole Position Deviation |
50-75μm |
|||||
Outline Tolerance |
Laser: +/-0.13mm |
|||||
Line Width/Spac Tolerance |
±20% |
|||||
Surface Treatment |
OSP/Immersion Gold/Nickel Plated Gold/Immersion Silver/Nickel Plated |
|||||
Thermal Stress |
7.3pmm/k |
Item2 | Attribute | ||
---|---|---|---|
Brand |
CeramTec / GTT / Huaqing / Laird / Maruwa / Rogers / Toshiba |
||
Base Material |
AI2O3 |
||
Base Material Thickness (exclude conductor) |
0.15-6mm |
||
Thermal Conductivity |
24-170W/mk |
||
Soldermask Type |
Aluminum Oxide |
||
Tg Value |
800℃ |
||
Halogen Free |
No |
||
Breakdown Voltage |
15 KV/mm |
||
Dielectric Constant (MHZ) |
9.4 (1MHz); 9.1 (13GHz) |
||
Water Absorption |
≤0.5% |
||
ROHS |
Yes |
||
Flammability |
Grade A |
||
Thermal Conductivity (W/m.K, or W/m.C) |
24-170 W/mk |
||
Dielectric Strength |
>15 KV/mm |
||
Wrap & Twist |
3% |
Prototype(<1m²) | Layers | Normal Service | Expedited Service |
---|---|---|---|
DPC Ceramic PCB |
1 Layer |
DPC: 2 - 3 weeks |
DPC: 1.5 weeks |
2 Layers |
DPC: 2 - 3 weeks |
DPC: 1.5 weeks |
Production | Layers | Normal Service | Expedited service |
---|---|---|---|
DPC Ceramic PCB |
1 Layer |
DPC: 3 - 4 weeks |
DPC: 1.5 - 2 weeks |
2 Layers |
DPC: 3 - 4 weeks |
DPC: 1.5 - 2 weeks |
LTCC ceramic PCBs (Low-Temperature Co-Fired Ceramic Printed Circuit Boards) have become a game-changer in the world of electronics. Their exceptional performance, reliability, and versatility have revolutionized various industries. In this article, we will delve into the applications of LTCC ceramic PCBs and highlight their potential to outperform traditional PCB solutions in different fields.
1. Aerospace and Defense
LTCC ceramic PCBs are widely used in the aerospace and defense industries due to their reliability, durability, and miniaturization capabilities. They are instrumental in satellite systems, avionics, missile guidance systems, and radar technology, delivering uninterrupted operation and precise functionality in harsh environments.
2. Automotive
With the rise of electric vehicles, LTCC ceramic PCBs are driving innovation in the automotive industry. These PCBs are ideal for power electronics, sensor modules, lighting controls, and other applications. Their high thermal conductivity, excellent electrical performance, and compact form factor contribute to more efficient and reliable automotive systems.
3. Medical Devices
LTCC ceramic PCBs have become a vital component in the development of advanced medical devices. Their biocompatibility, high-frequency capabilities, and miniaturization potential enable the creation of implantable medical devices, diagnostic equipment, and wearable health monitoring systems. These PCBs empower medical professionals to deliver precise diagnoses and improved patient care.
4. Internet of Things (IoT)
LTCC ceramic PCBs play a crucial role in the Internet of Things (IoT) by providing the foundation for connected devices. Their high integration density, RF compatibility, and low power consumption make them essential for smart homes, industrial automation, and environmental monitoring systems. LTCC ceramic PCBs bring us closer to a fully connected world.
5. Telecommunications
In the telecommunications industry, LTCC ceramic PCBs offer unmatched performance and reliability. They are used in base station modules, RF amplifiers, microwave filters, and wireless transceivers. These PCBs ensure seamless communication, enabling the evolution of 5G networks and beyond.
6. Industrial Applications
LTCC ceramic PCBs are driving innovation in the industrial sector by increasing efficiency, productivity, and automation. They are used in power electronics, motor controls, sensor interfaces, and control systems. These PCBs provide exceptional thermal management, power handling capabilities, and reliability, supporting the development of advanced industrial machinery and smart factory environments.
DPC Ceramic PCB Specification:
Substrate material: |
96% Al2O3 |
Board thickness: |
0.635mm+/-0.1mm |
Conductor: |
35um copper |
Solder mask: |
N/A |
Silkscreen: |
N/A |
Surface finishing: |
ENEPIG 3u’’ |
Application: |
Sensor |
Background:
Best Sensors is a leading technology company specializing in the development of advanced environmental monitoring solutions. They are known for their innovative sensor products used in various industries such as industrial automation, smart cities, and agriculture. Best Sensors has been experiencing challenges with their current sensor design, specifically in terms of thermal management and signal integrity. They are seeking a solution to reduce dielectric loss of their sensors.
PCB challenge:
- They have a very thin thickness and the single size also is very small, it will be broken easily.
- Due to the single piece has small size, the silkscreen on the PCB is not easy to print well, some will be illegible.
- Customer requires ship by panel, total 91pcs in 1panel and the X-out boards should less than 3pcs, it is not easy to control.
Solution:
Recognizing the specific challenges faced by Best Sensors, we recommended integrating DPC ceramic circuit boards into their sensor design. DPC ceramic circuit boards possess high thermal conductivity, excellent insulation properties, and precise circuitry, making them ideal for addressing the thermal management, signal integrity and dielectric loss issues faced by Best Sensors.
We worked closely with their engineering team to understand their specific requirements and design constraints. They collaborate on developing a customized DPC ceramic circuit board solution that seamlessly integrates into the sensor modules. The DPC ceramic circuit boards provide efficient heat dissipation, ensuring stable sensor performance even in demanding operating conditions. The high-quality circuitry enables accurate signal transmission and reduces electromagnetic interference, resulting in improved overall sensor reliability and performance.
Result and Benefits:
The integration of DPC ceramic circuit boards has exceeded their expectations, Best Sensors expresses their satisfaction with the solution provided by us. They greatly appreciated the expertise and collaboration exhibited by our team throughout the design and implementation process.