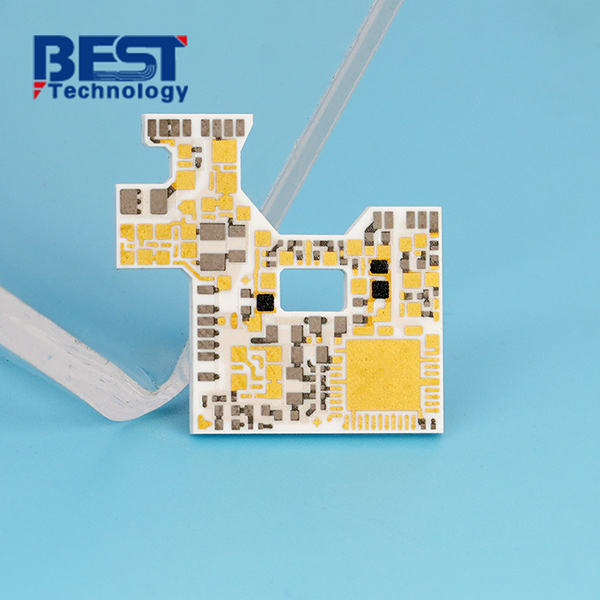
LTCC Ceramic Substrate PCB For Vehicle Electronics






Board Thickness: 0.635mm+/-0.1mm
Conductor: 10-15um AgPd 3-5mm Au
Solder Mask: N/A
Silkscreen: N/A
Surface Finishing: N/A
Application: Vehicle Electronics
Item1 | LTCC Capabilities | |||||
---|---|---|---|---|---|---|
Layer Count |
4-64 Layers |
|||||
Max Board Dimension |
150mm×150mm |
|||||
Min Board Thickness |
Single layer 0.1mm, total thickness 0.15mm |
|||||
Max Board Thickness |
Single layer 0.25mm, total thickness 6mm |
|||||
Conductor Thickness |
6-12μm (the surface layer can be thickened to 80μm) |
|||||
Min Line Width/Line Space |
150μm (surface layer can be refined to 50μm) |
|||||
Substrate Type |
Al2O3 |
|||||
Substrate Thickness |
0.15-6mm |
|||||
Min Hole Diameter |
100μm |
|||||
Min Hole Spacing |
250μm |
|||||
Min PAD Ring(Single) |
0.125mm |
|||||
PTH Wall Thickness |
N/A |
|||||
Min Solder PAD Dia |
0.1mm |
|||||
Min Soldermask Bridge |
75μm |
|||||
Min BAG PAD Margin |
0.635mm |
|||||
PTH/NPTH Dia Tolerance |
10μm |
|||||
Hole Position Deviation |
30-40μm |
|||||
Outline Tolerance |
Laser cutting: 0.005; Die stamping: 0.005 |
|||||
Line Width/Spac Tolerance |
±20% |
|||||
Surface Treatment |
Immersion Gold/Nickel Palladium Gold (Surface treatment is not recommended) |
|||||
Thermal Stress |
7.3ppm/K |
Item2 | Attribute | ||
---|---|---|---|
Base Material |
DP951,DP9K7, Ferro-A6-M |
||
Base Material Thickness (exclude conductor) |
0.15-6mm |
||
Thermal Conductivity |
17W/mk |
||
Soldermask Type |
Aluminum Oxide |
||
Tg Value |
800℃ |
||
Halogen Free |
No |
||
Breakdown Voltage |
9.4 (1MHz); 9.1 (13GHz) |
||
Dielectric Constant (MHZ) |
≤0.5% |
||
Water Absorption |
0% |
||
ROHS |
Yes |
||
Flammability |
Grade A |
||
Thermal Conductivity (W/m.K, or W/m.C) |
17W/mk |
||
Dielectric Strength |
15KV/mm |
||
Wrap & Twist |
0.003 |
Prototype(<1m²) | Layers | Normal Service | Expedited Service |
---|---|---|---|
LTCC Ceramic PCB |
6 Layers |
6 - 8 weeks |
3 - 4 weeks |
8 Layers |
6 - 8 weeks |
3 - 4 weeks |
|
10 Layers |
6 - 8 weeks |
3 - 4 weeks |
|
>10 Layers |
6 - 8 weeks |
3 - 4 weeks |
Mass Production | Layers | Normal Service | Expedited service |
---|---|---|---|
LTCC Ceramic PCB |
6 Layers |
7 - 9 weeks |
4 - 5 weeks |
8 Layers |
7 - 9 weeks |
4 - 5 weeks |
|
10 Layers |
7 - 9 weeks |
4 - 5 weeks |
|
>10 Layers |
7 - 9 weeks |
5 - 6 weeks |
What we can serve you?
At Best Technology, we strive to be your reliable partner, delivering high-quality PCB manufacturing services while prioritizing customer satisfaction.
-
Quality Assurance
We have certifications like ISO9001, ISO13485, IATF16949, UL, ROHS and CE, ensuring standardized and high-quality PCB manufacturing. Our advanced equipment and skilled technicians conduct thorough inspections to meet industry standards.
-
No MOQ Requirement
Whether you need 1 pcs ceramic PCB or more, we cater to orders of any size, saving you unnecessary expenses.
-
On-time Shipping
We work in three shifts to maintain a 99% on-time delivery rate. You can choose reliable courier services like DHL for speedy and budget-friendly shipping.
-
24/7 Hour Customer Service
Our dedicated customer service team is available round the clock to address your inquiries and provide assistance.
-
Customer Complaints and Refunds
We have a customer complaint department to handle any issues. If you're unsatisfied, we offer options for refunds or re-production, and we welcome feedback to improve our services.
Background:
Recently, we received a request from Electra Motors, an electric vehicle manufacturer, to develop a ceramic PCB for their advanced power electronics. Electra Motors aimed to improve the electrical performance and reliability of their electric vehicles.
PCB Challenge:
Electric vehicle power electronics require high power density and efficient thermal management. The existing PCBs in Electra Motors' vehicles were unable to withstand the demanding operating conditions, leading to performance degradation and reliability issues.
Solution:
Understanding the challenges faced by Electra Motors, our team proposed utilizing aluminum nitride as the base material for the ceramic PCBs. Aluminum nitride exhibits excellent thermal conductivity and superior electrical insulation properties, making it ideal for power electronics applications. We optimized the design by carefully selecting trace widths and implementing a multilayer structure to accommodate the high-power density requirements.
Result and Benefits:
After implementing the ceramic PCBs in Electra Motors' electric vehicles, significant improvements were observed. The aluminum nitride PCBs efficiently dissipated heat, ensuring optimal performance and preventing overheating-related failures. The enhanced electrical properties of the ceramic PCBs resulted in improved power conversion efficiency and overall vehicle reliability. Electra Motors commended our professionalism and acknowledged the innovative solution we provided. They expressed their intent to continue partnering with us for future ceramic PCB requirements in their electric vehicles.