The field of electronics is rapidly evolving, with new technologies and materials emerging all the time. One of the most exciting and promising developments in recent years has been the rise of HTCC (High-Temperature Co-FiCo-firedmic) PCBs. These advanced printed circuit boards offer unparalleled performance and reliability, making them a critical technology in a wide range of industries, from aerospace and defense to medical devices and automotive electronics.
What is HTCC Ceramic PCB?
HTCC (High-temperature Co-fired Ceramic) PCB is made from a ceramic substrate rather than traditional fiberglass. It is met by printing a high melting point metal heat resistance paste, which includes tungsten, molybdenum, manganese, and other metals, onto a flow ceramic green billet with 92-96% alumina content. A sintering agent of 4-8% is added, and the billet is then laminated to create a multilayer structure.
This substrate is co-fired under high temperatures around 1500-1700oC that is capable of withstanding extreme temperatures and harsh environments. Conductive and resistive materials are deposited onto the substrate using a specialized thick-film printing process, creating a solid and stable PCB that can perform reliably even under the most demanding conditions.
Conductor Material for HTCC Ceramic PCB
In the electronic market, the most common conductors for ceramic circuit boards are gold, silver, copper and other lower melting point metal materials. In comparison to normal DPC or DBC ceramic board, due to the high firing manufacturing temperature, HTCC ceramic PCB can’t use these metal materials, because they have low conductivity and will cause signal delay and other defects, so it is not suitable for high-speed or high-frequency micro-assembly circuit substrate.
After several years researching and analyzing, it has been proved high melting metal materials are ideal for HTCC conductor, for example: Tungsten, Molybdenum, Nickel, Manganese, Platinum, and other refractory metal materials. The reasons are showing as below:
As we know, the mainly ceramic substrates for HTCC are aluminum oxide (Al2O3), mullite (mainly for Al2O3-SiO2) and aluminum nitride (ALN).
a) In generally, the micron grade α-Al2O3 sintering temperature > 1550℃, and based on the different of the raw material particle size, sintering additives, the actual sintering temperature will be change as well.
b) While ALN is a covalent compound with a small self-diffusion coefficient, so it is very difficult to sintering densification. In order to solve this problem, rare-earth metal oxides and alkaline-earth metal oxides are usually used as sintering additives to promote sintering. But even so, the sintering temperature still needs to be over 1800℃.
With so high sintering temperature, then the conductor material for HTCC ceramic PCB needs to meet these two key points:
1.The conductor metal can withstand high temperature, so from the melting point, the general requirement is not less than 1700oC.
2.The metal material will not react with Al2O3 and ALN at high temperature.
So in conclusion, the tungsten, molybdenum, nickel, manganese and platinum are suitable for high temperature co-firing (HTCC) ceramic circuit board.
Ceramic Substrate Selection for HTCC
The common HTCC ceramic circuit are Al2O3 ceramics, ALN ceramics and Mullite ceramics. The different material composition of HTCC determines its different applications, and the corresponding material shortcomings also limit its applications in some way. So choose a right material for your HTCC ceramic is most important.
Al2O3 (aluminum oxide)
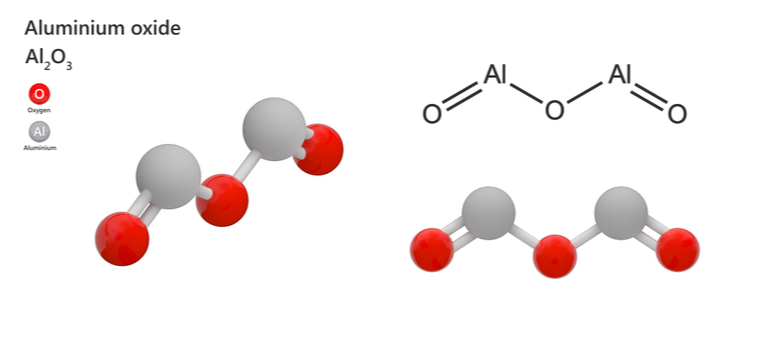
During sintering, the ceramic particle becomes a dense material and the sample shrinks by approximately 15% to 20%. Among them, in the field of ultra-high temperature, 99.99% Al2O3 HTCC ceramics are the most widely used. Some basic material property parameters of HTCC Al2O3 ceramic boards are shown in the figure below:
The Al2O3 HTCC ceramic manufacturing technology is gradually mature, the cost of dielectric is relatively low, the thermal conductivity and bending strength is high as well. However, there are also some disadvantages to aluminum oxide HTCC, details below:
(1) Its dielectric constant is too high, which will prevent the improvement of signal transmission speed.
(2) The conductor resistivity is high, resulting the large signal transmission loss.
(3) The coefficient of thermal expansion differs greatly from that of silicon, thus limiting its application in supercomputers.
ALN (aluminum nitride)
For aluminum nitride substrate, its dielectric constant and dielectric loss are better than aluminum oxide due to its high thermal conductivity and thermal expansion coefficient matching with semi-conductor materials such as Si, SiC and GaAs. Meanwhile, ALN is a hard substrate, so that enables it work well under harsh environment.
The disadvantages of using aluminum nitride substrate are:
(1) Wiring conductor resistivity is high, causing the large signal transmission loss.
(2) High sintering temperature, makes it has large energy consumption.
(3) The thermal conductivity of aluminum nitride substrate decreases after co-firing with tungsten, molybdenum and other conductors.
(4) Screen printed resistors and other passive components cannot be incorporated into the high-temperature co-firing process, because the metal oxides in the slurry of these passive components will react in the process of reducing atmosphere and deteriorate the performance.
(5) The outer conductor shall be plated with nickel gold to protect it from oxidation, while increasing the surface conductivity and providing a metallized layer capable of wire welding and soldering component mounting.
Although there are these shortcomings, but generally speaking, aluminum nitride substrate has more advantages compared to other HTCC ceramic substrate, and it has a good development trend in the field of high reliable and high-temperature applications such as sensor packaging, surface mount packaging, MEMS packaging, optical communication packaging, LED packaging and so on.
Mullite
Mullite has a dielectric constant of 7.3-7.5, while aluminum oxide (96%) has a dielectric constant of 9.4, which is higher than mullite. Therefore, mullite has a signal transmission delay about 17% less than aluminum oxide. Moreover, Mullite has a thermal expansion coefficient similar to silicon, so this substrate material has been developed rapidly.
For example, Hitachi, Shinko and other companies have developed mullite multilayer ceramic substrate, and their products have good performance indicators. However, the wiring conductor of this substrate can only be tungsten, nickel, molybdenum, etc., and the resistivity is larger and the thermal conductivity is lower than that of alumina substrate.
Why HTCC Use Air or Reduction Atmosphere for Sintering?
Almost of conductor materials of HTCC ceramic belong to the base metals, and its cost is relatively low. However, they have a common drawback – They are easily be oxidized at high temperatures.
In the air, Tungsten oxidizes rapidly from 350℃, and Molybdenum is oxidized slowly at 520℃ to form molybdenum trioxide (Mo2O3). When the temperature rises over than 600℃, molybdenum will be oxidized into molybdenum trioxide (MoO3) in a quick speed. Nickel begins to oxidize at 400℃, while Manganese is more active and can be combined with oxygen when heated to form manganese dioxide (MnO2). Therefore, when using such materials for co-sintering, a reducing atmosphere needs to be added to ensure that the conductor won’t be oxidized. In general, the added atmosphere is hydrogen.
Besides, the remaining platinum (Pt) is a precious metal. It has a very stable chemical property, insoluble in strong acid and alkali solutions and won’t oxidize in the air. Therefore, platinum, as a metallic conductor, can be directly co-sintered with ceramics in an air atmosphere. At the same time, Platinum also has excellent catalytic properties that other conductor metals without, which gives it some special uses in some applications.
How to Get a Good Quality HTCC Ceramic PCB
To ensure the highest quality HTCC ceramic PCBs, it is important to work with a manufacturer that has experience and expertise in this specialized technology. Look for a manufacturer that has a proven track record of producing high-quality HTCC ceramic PCBs for a range of applications. They should be able to provide detailed information about their manufacturing process and quality control procedures, and should be willing to work closely with you to ensure that your specific needs are met. BSTCeramicPCB has authorized by ISO9001 quality control system, ISO13485 and IATF16949. All the manufacturing steps are in conform to the quality control system. We can be sure your most reliable HTCC ceramic board vendor in China.